Mechatronics - Robot Battles
January - May 2024
I took a sumo robotics class this semester and built a torque maximizing, center of gravity lowering, opponent capturing and enemy plowing mechatronic robot. Say that 5 times fast.
The mechatronics class is a 16 week long course where the first half is devoted to learning the mechanics and electronics (hence mechatronics) that go into sumo robots, and the second half is all about building and testing one.
For our competition, we had many constraints to follow. Size, no larger than 10”x10”x6”; Weight, less than 5 lbs; Cost, less than $200; Motor stall current, max 3A; Battery; 12V rechargeable non-lithium-ion no lead-acid battery, only defensive strategy and design.
Strategy & Mechanical Design
We had 4 major design pillars.
Plowing Mechanism
Maximizing Torque
Low Center of Gravity
Opponent Capture System
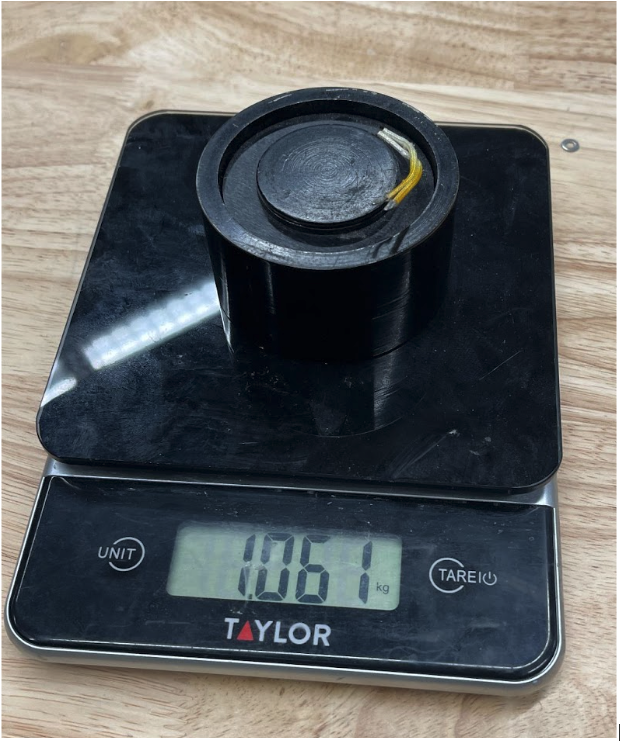
Plowing Mechanism: Simple low angle attack to get opponents into the air, making it easier to push them out of the ring.
Maximizing Torque: More torque means more pushing power. Torque is influenced by normal force, rolling friction (static friction), and mechanical gear ratio.
Low Center of Gravity: Harder for opponent to plow robot, more traction, more control.
Opponent Capture System: Cheese grater but for opponent robots. Aim is to get other robots stuck in our mesh and optimize robotic bullying.
Electronics
Aside from CADing the design and 3D printing the components, there was also a lot of work that needed to be done on the electronics side. The robot needed to detect the boundaries of the competition arena and make sure not to go out of bounds. So, we used a relay / logic system that communicated IR sensor signals to an ATMega328P then to a motor controller then finally to the two motors (the robot is dual wheel).
Microchip, MDriver, IR Sensors, Battery, & Motors
Programming of the ATMega
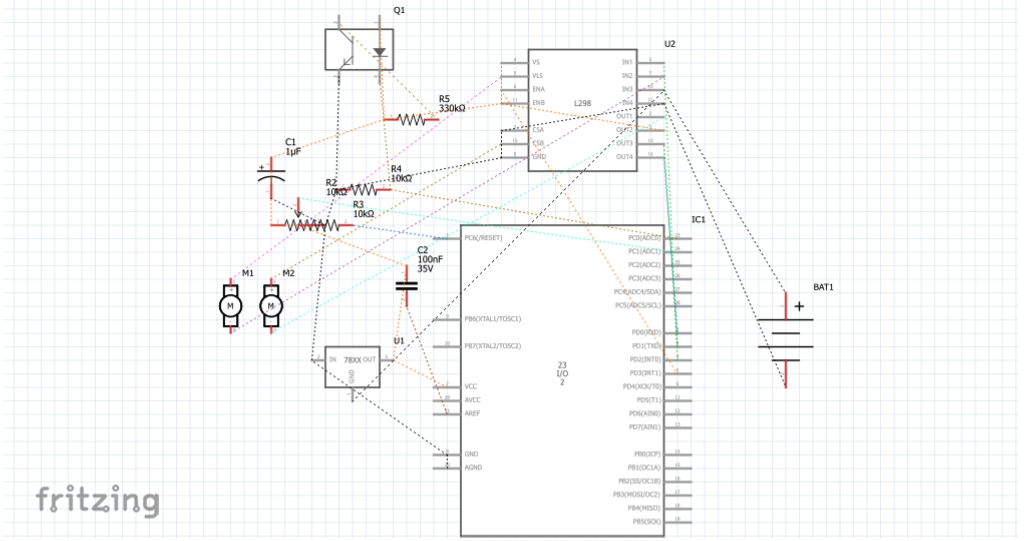
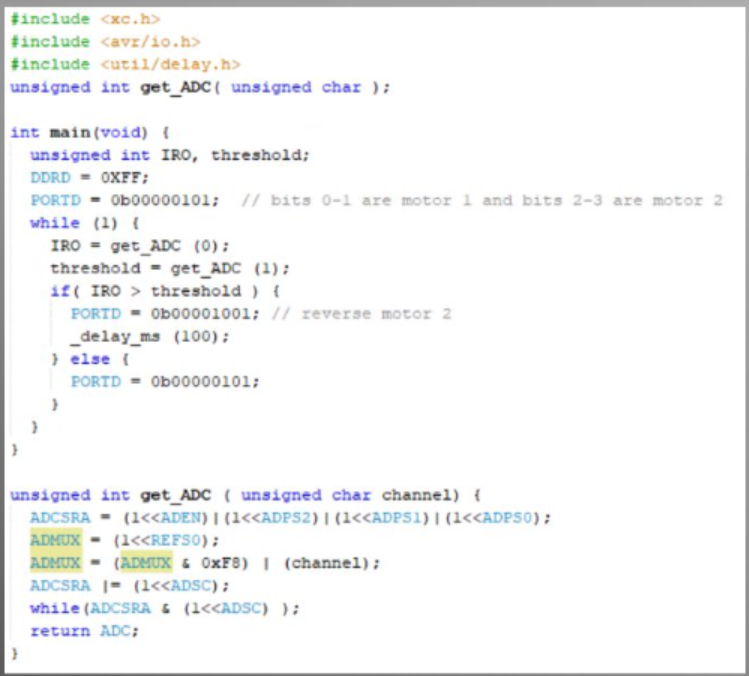
Assembly was used to flash the SNAP Programmer. MDE lab x IPE program in C language used to program ATMega328P microcontroller connected to SNAP programmer.
IR Sensors (OPB743wz)
- 890 nm emitter
- 7.62mm range
Fixes
This project had quite a few issues that needed to be worked out.
IR Sensor Calibration
The IR sensors are meant to detect the boundaries of the mat which are covered in white tape. The normal bounds are covered in black tape. A cat and mouse game of calibrating the IR sensors to perfectly react to a change in which tape it was over was crucial for finding the goldilocks of performance.
Here’s what it shouldn’t do.
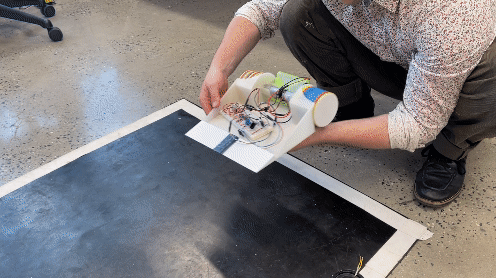
And here's what it should do.
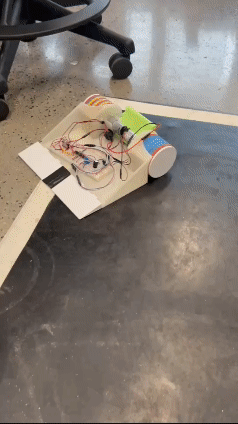
Honeycomb Design
A common question that gets asked in engineering, is how can I maximizing the structural strength of a certain material while also minimizing my material usage? The short answer is, it depends. That’s actually why engineering exists in the first place, if there was a straight forward answer to that question the professional of engineering would just be a niche profession like theoretical mathematics or something. Back to the question, there is actually an answer other than “it depends.”
Of course I wanted my robot to be the next Ali, so I thought honeycomb would be good for this.
I made a couple test prints to see how this would translate to the real world and althought it looks cool, I found out it wasn't as optimal as it could be.
A mechatronics robot is expected to have isotropic load resistance (meaning it should be able to take punches from any direction). Now typical load resistance strategies that you’ve seen are probably in static civil infrastructure. Bridges, buildings, that sort of thing. For the most part these structures only need to deal with gravity. So they are built to be extremely tolerant in the vertical direction. An isotropic load resistance infill that I found to be effective is the Gyroid Infill at around 15%.
End Performance
The Egg Roll Robot (devilishly cunning nickname) successfully detected the sumo ring edges, and consistently completes a turn to avoid driving out of the ring. The final sumo robot battle was canceled due to student protests. Apologies for not having sumo robot battle content.