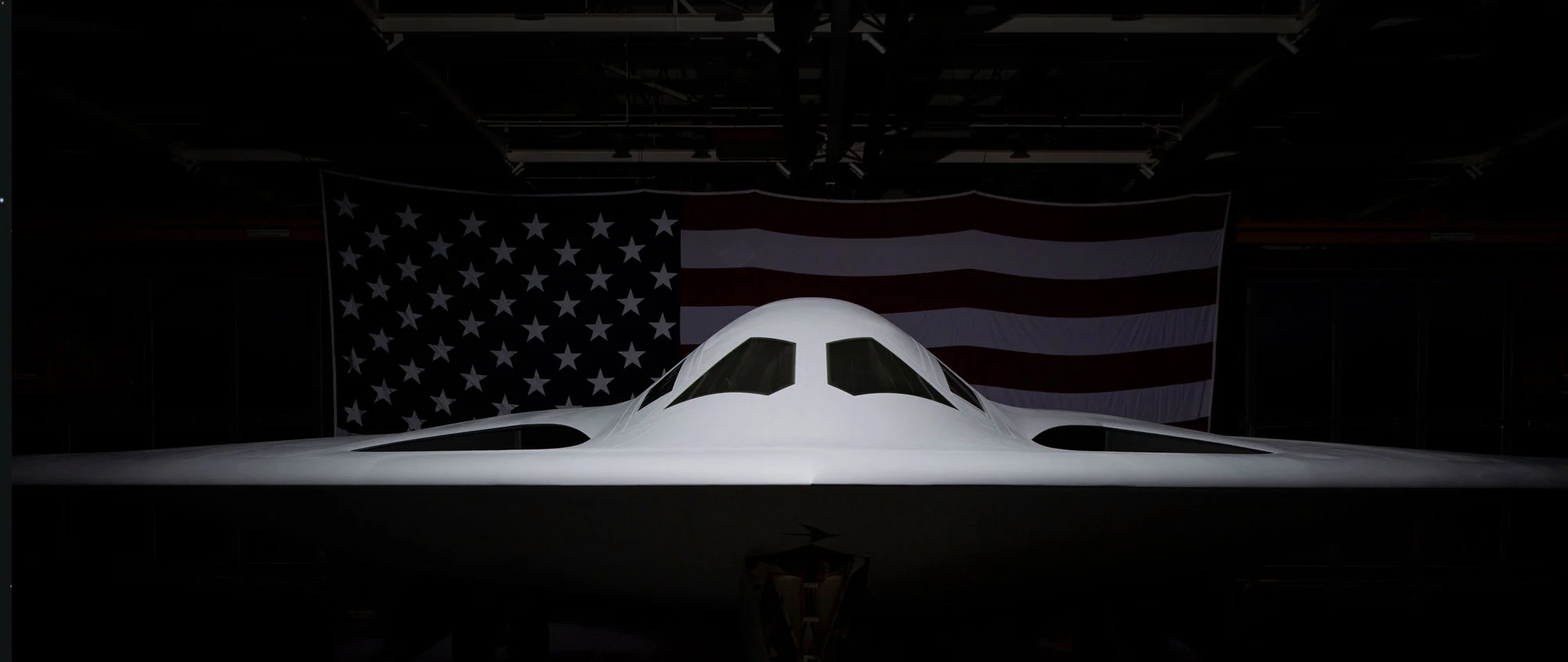
Experiences - Northrop Grumman
May 2023 - August 2023 | Baltimore, Maryland
Advanced Microelectronics & Solid Mount Technology Manufacturing
Northrop Grumman’s brand has meaning and value in the marketplace, and therefore I have a responsibility to properly represent the brand and the company in external communications. If you are interested in the company values, you can find them here.
With that being said, all of the below opinions are of my own and I am not writing on behalf of Northrop Grumman.
Introduction
Working at Northrop Grumman (NG) this summer was an absolute pleasure. I had the chance to meet so many people all the way from first year interns like myself to people who have spent 60+ years working in the industry. I was placed into the Manufacturing Group where I supported and developed production assemblies of high-quality mission-critical systems for the Advanced Microelectronics Cell, Solid Mount Technology, and the automated feed factory which produces airborne/space radar.
Work Atmosphere
The Northrop Grumman work atmosphere is very positive and collaborative. For people who want to work really hard, there are tons of opportunities to show your hard work and climb the ladder and gain more responsibilities. And for people who have a life outside of work (family, hobbies, social life, etc.) and don’t have the capability to devote all their time to the company, the workflow can be very accommodating of that. The company has generous PTO, paternal/maternal leave, jaw dropping benefits, and many more. I have no doubt this is the reason NG has found so much success. What’s really surprising is that interns are given 401k matching up to around 6%. Most companies wouldn’t do this and it goes to show how much NG cares about their interns.
At NG, most people (including myself) work on what’s called a 9/80 work schedule. Where everyone works 9 hours each day in return for every other Friday off. It’s a great system and it again emphasizes the work-life balance NG has for its employees.
Some jobs and companies have very cutthroat and horrible company cultures that lead to toxic work environments, however NG is literally the complete opposite. Everyone there wants to be helpful and support you no matter what.
What I did
A lot of the work I did there is proprietary so I can’t go into the exact details. However, I can talk about the general processes and softwares I used.
Northrop Grumman has facilities all over the US and I worked at one called Mission Systems (MS). I specifically worked in the manufacturing of airborne/space radar. One thing everyone underestimated when learning about this technology is how strict and meticulous military/space manufacturing guidelines are. But, it makes total sense, there’s no room for error on a battlefield and certainly no error when sending equipment into space. You get one shot to make sure everything is made correctly, and your clients are military entities.
Because of these strict guidelines, the parts we manufacture are put through extensive quality and performance tests after they have been manufactured, leading the team to make sure all the manufacturing processes are as efficient and accurate as possible. With this comes the need for data analysis and data architecture.
My time was spent setting up data architecture and infrastructure for principal engineers to better access and help make better educated decisions to optimize the manufacturing process. I worked closely with hardware to software integration of 3D AOI and RPA processes. The programs I worked on were classified, so I have no knowledge of where the components would go for the final product.
I am most proud of making an entirely new inspection process for a specific manufacturing assembly. This new inspection process is estimated to reduce cost and time by 93% and has the potential to change the way NG does inspection processes.
Finally, the interns presented our work for the summer in an End of Summer Showcase to a large audience. I was able to present my new inspection process to directors, vice presidents, and managers of the BWI facility as well as answer any questions they had for possible implementation.
Networking opportunities
Throughout the internship I went on many tours of the facility, which gave me a great understanding of the general start to finish process for products at MS. And now that I knew MS from a macroscopic perspective, I wanted to dive into it with a microscopic lens.
So, I started cold emailing people from the company directory who had cool sounding job titles. The response rates varied but the majority would respond and were eager to meet me in person and show me what they did/facilities they worked in. By the end of my internship, I met with around ~20 employees, each with their own niche/interesting jobs. I made sure to always send a thank you email afterwards and add them on LinkedIn to keep in touch in the future. I noticed that the younger the employee I reached out to was, the more likely they were to respond to my emails. And the harder they were to get in contact with, the better advice they usually gave.
Knowing many people at MS gives me the ability to return to almost any section of the facility if I want to come back for another internship.
Thank You NG
I loved the internship so much that I extended the internship to 11 weeks. Thank you to everyone who made this internship possible, including Kaitlyn Walton and Ted May.
Image Credits: Northrop Grumman Corp.